
The history of porcelain started in 1883 when pottery industry was started in one of the streets of Belarus.

In 1920 the factory was owned by the
Minsk city council of workers and soldier’s deputy. The enterprise was
developed fast that time.

After Minsk was freed from the Nazi
occupants the factory had to be reconstructed. In 1946 it started
producing angular glazed and unglazed tiles.

A gas generator was exploited in 1950
making ceramic baking more successful. Qualitative changes of
technological processes lead to re-profiling of the factory that was now
busy with porcelain making. 15 March 1951 is the birthday of Belarus
porcelain.

The mechanized plant that had to produce 5,4 million pieces of cutlery was put into effect in 1979.

A block of additional works with the
area of 6000 square meters was put into effect in 1983. The factory
continued its development till 1990.

Today the following works are located on
the territory of the factory: hollow construction shop, flat
constructions shop, radioceramics shop, firebrick shop and laboratories.



The factory was closed in 2009. According to the official reason, it operated at a loss for many years.

Year of production 1977, item number 8, order number 2031210, mass 5157 kg (11370 ft).
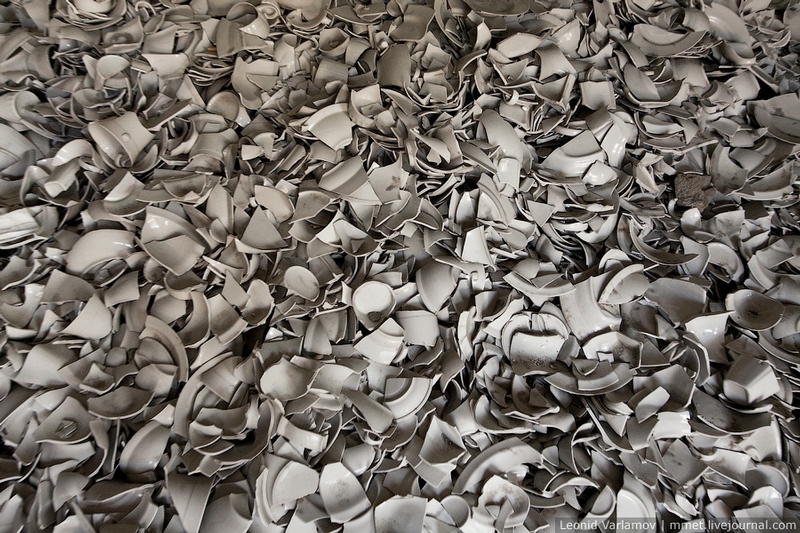
Broken items are used in production of fresh molding material.
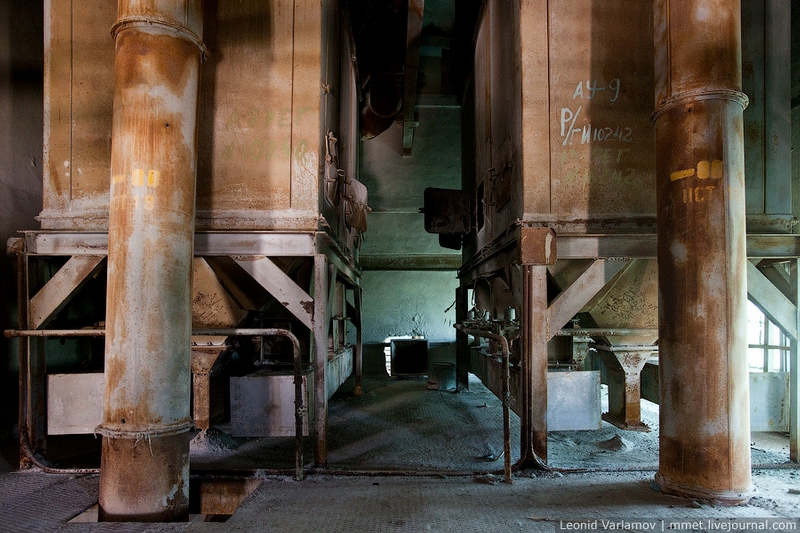
The raw material is taken to the factory
by car. Kaolin contains electrolytes and coagulants that can negatively
influence the quality of porcelain items. That is why it is cleaned and
goes through the stage of filtration.
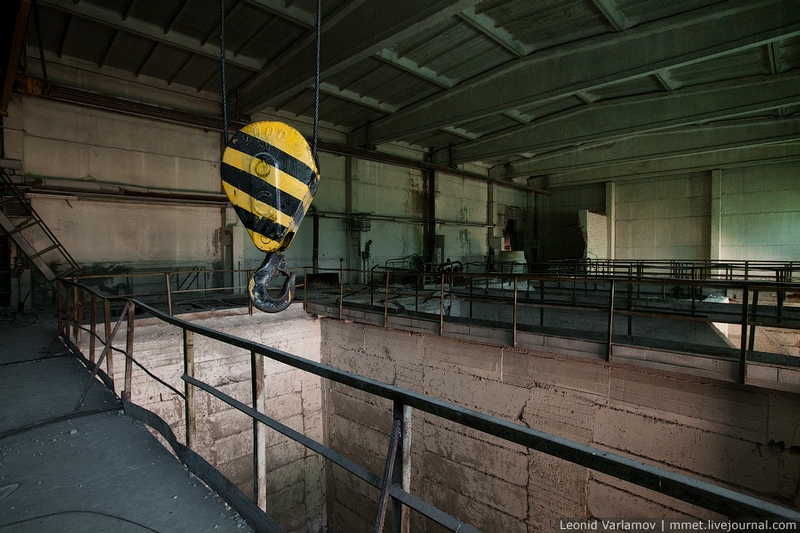
Quartz sand is sifted, can be dried in case of high humidity and then loaded into a drum.
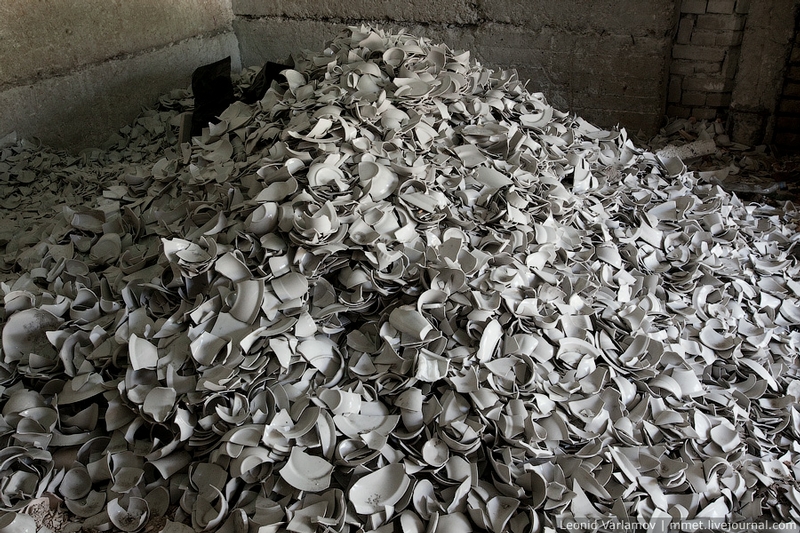

Flat constructions are formed in
submachines. They are cut into 20-25 pieces in one movement. Then the
item is put into an empty mould heading to the forming roller. The
steering circle rotates counterclockwise and stops every 90 degrees. The
mass is moved together with the mould and this is how an object is
made.
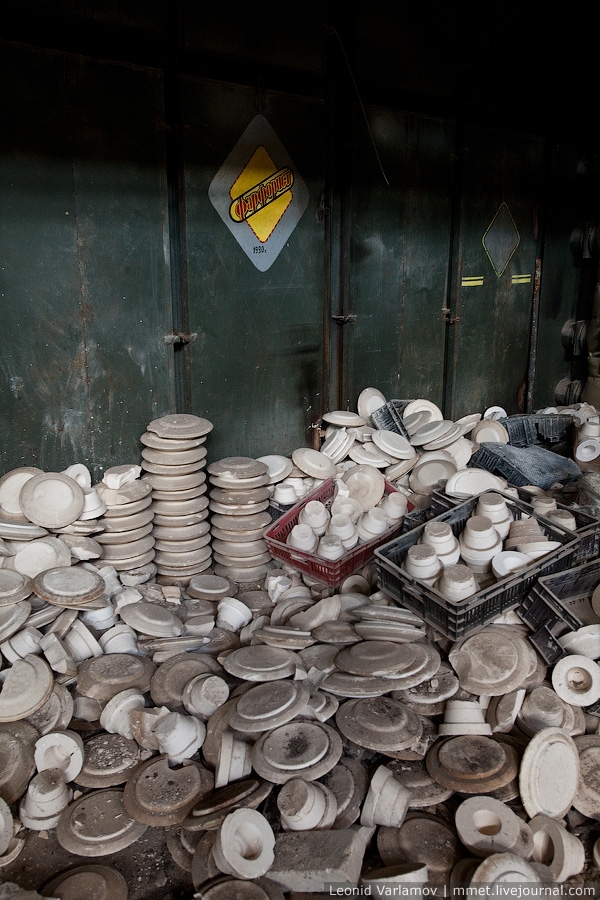
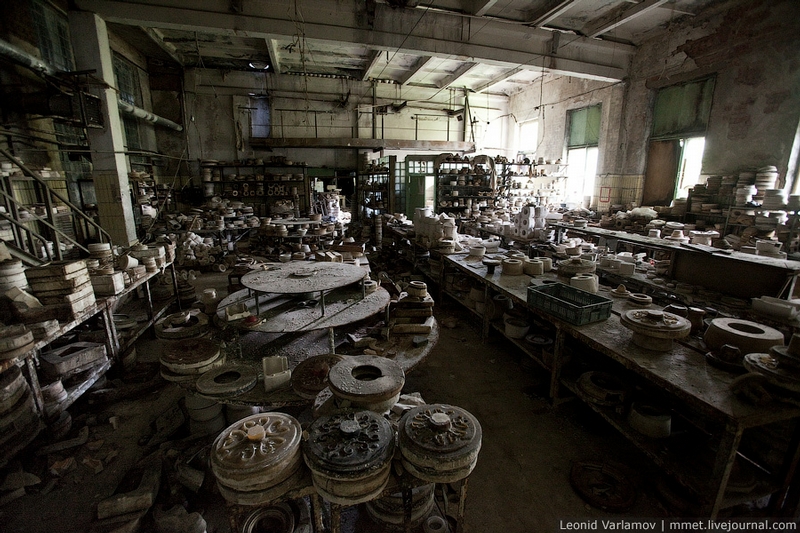
The forming roller is heated to prevent adhesion of the mass. Flat and hollow items have different mould forms.
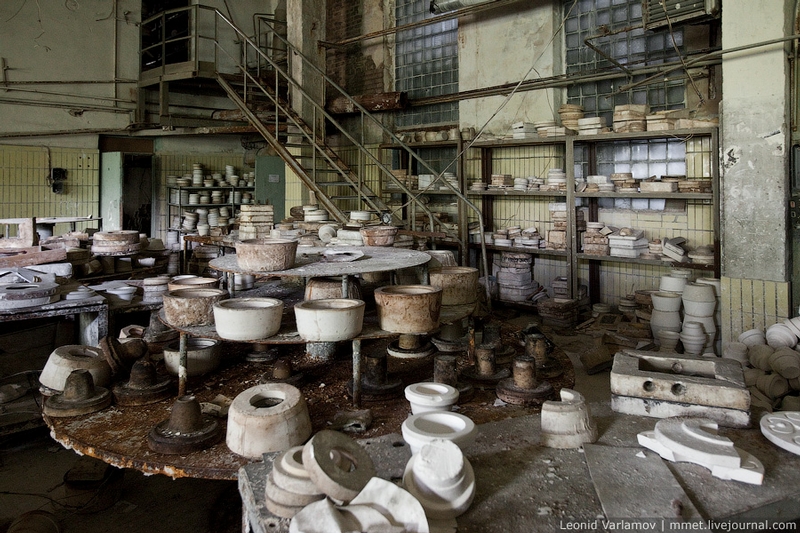
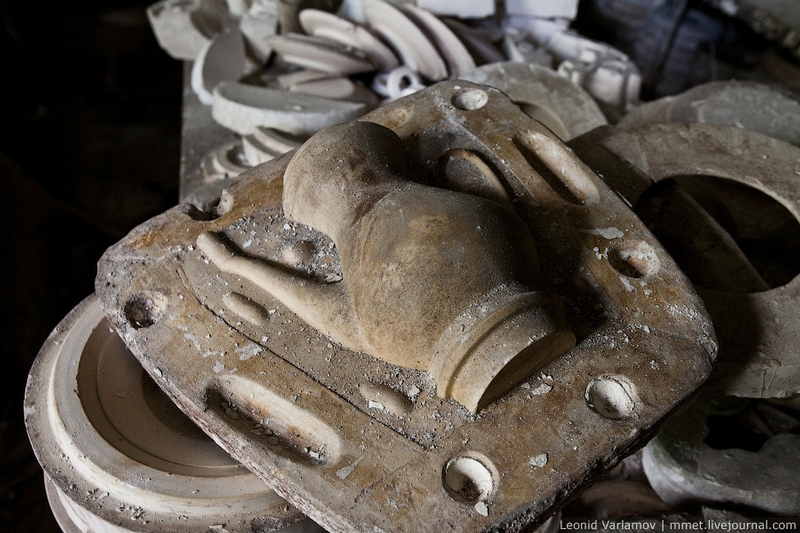
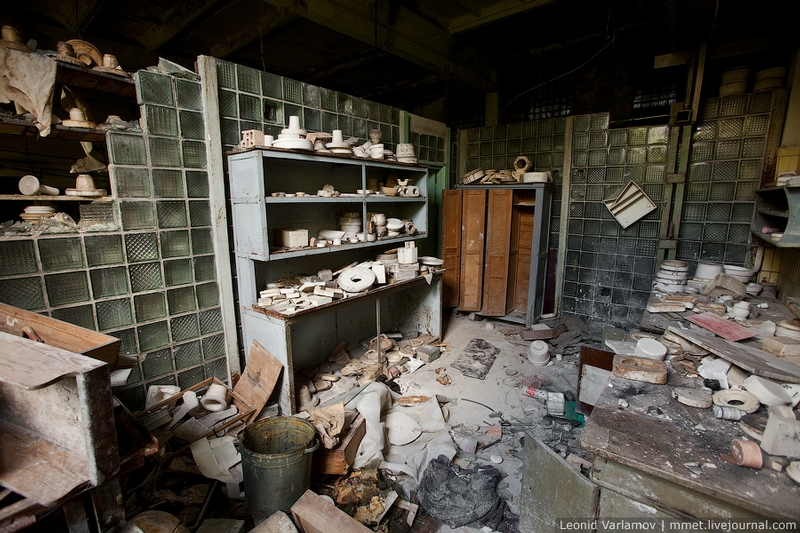
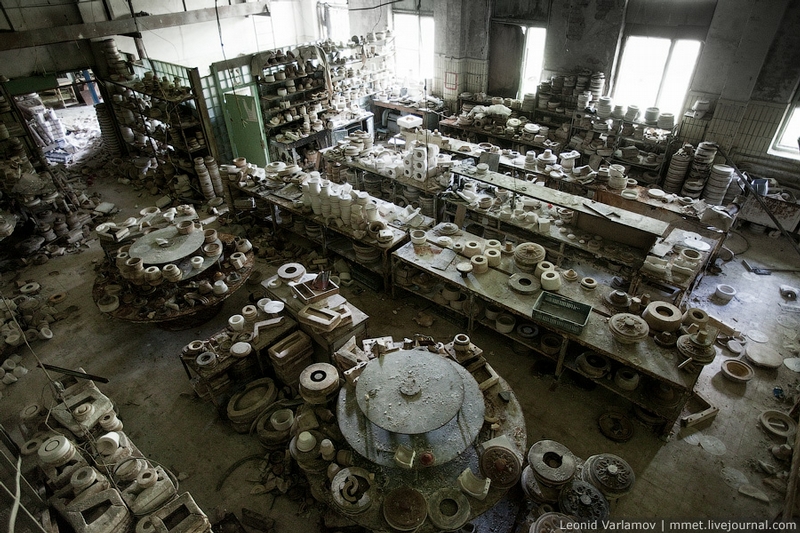
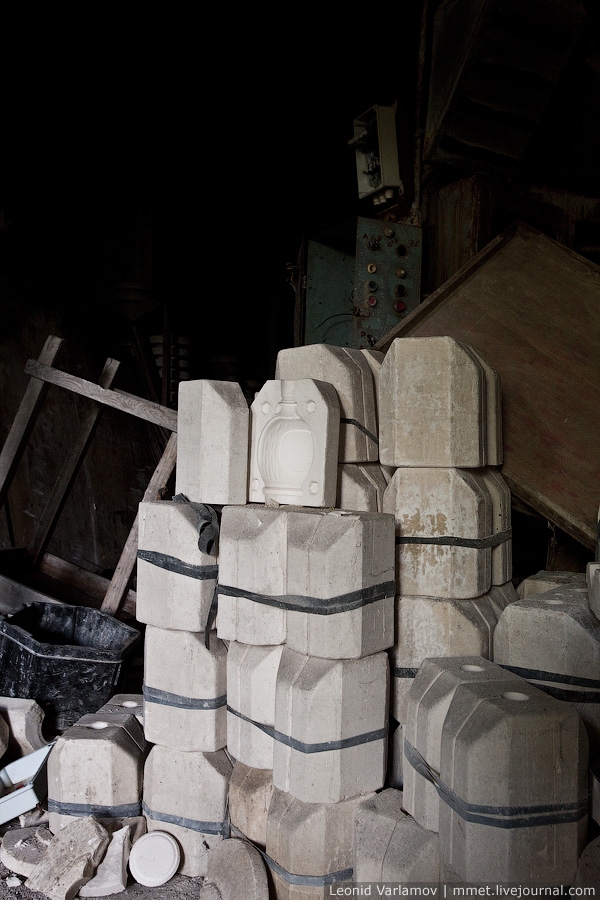
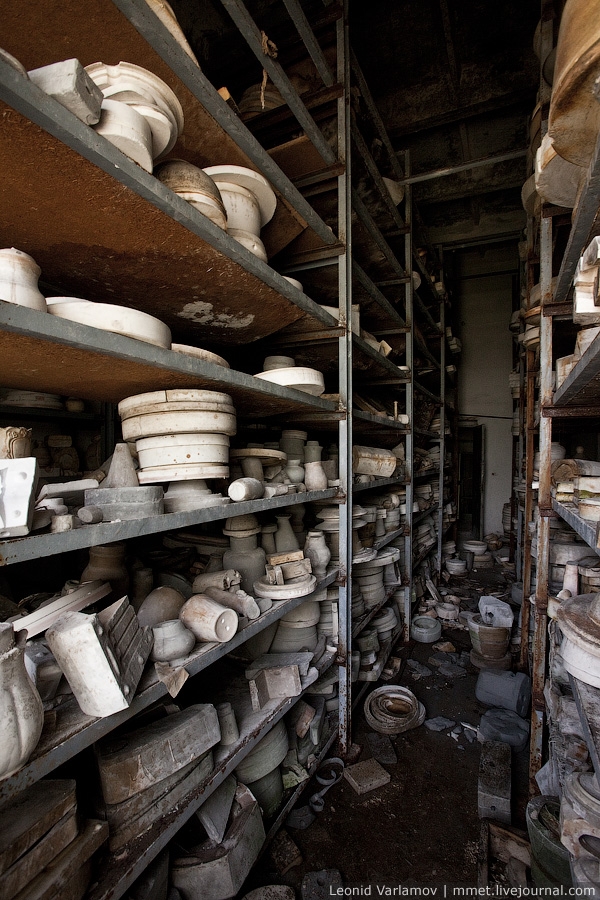
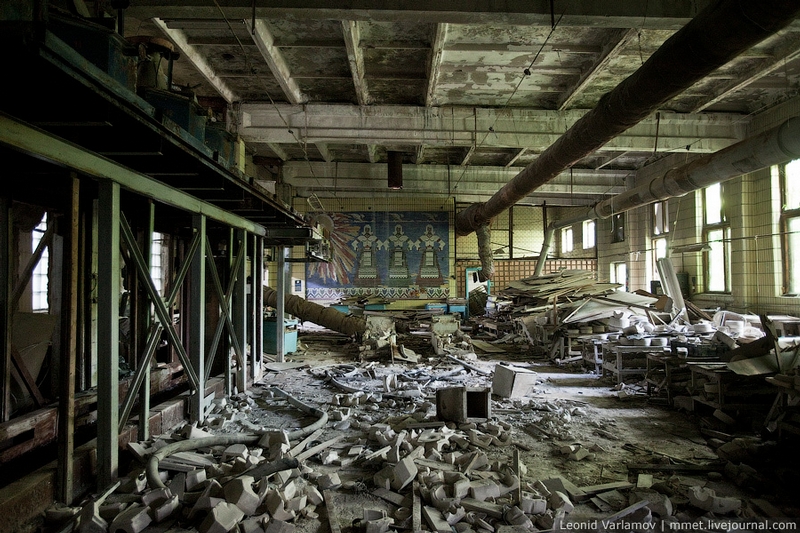

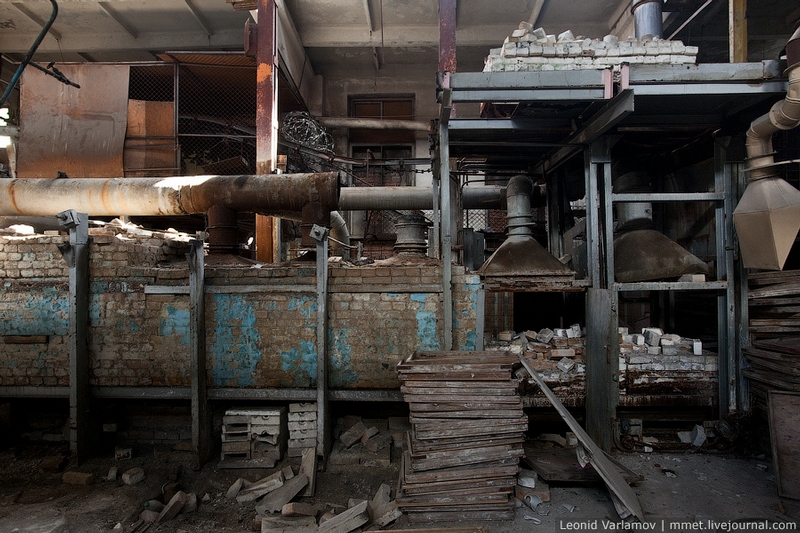

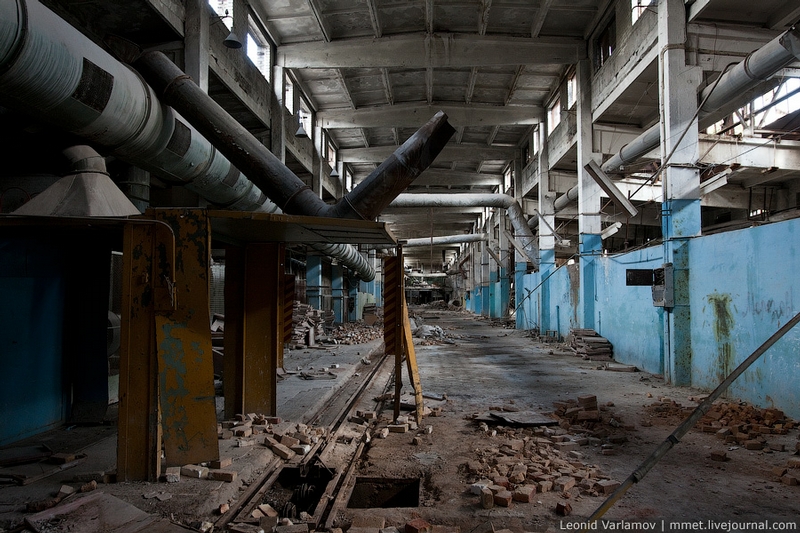
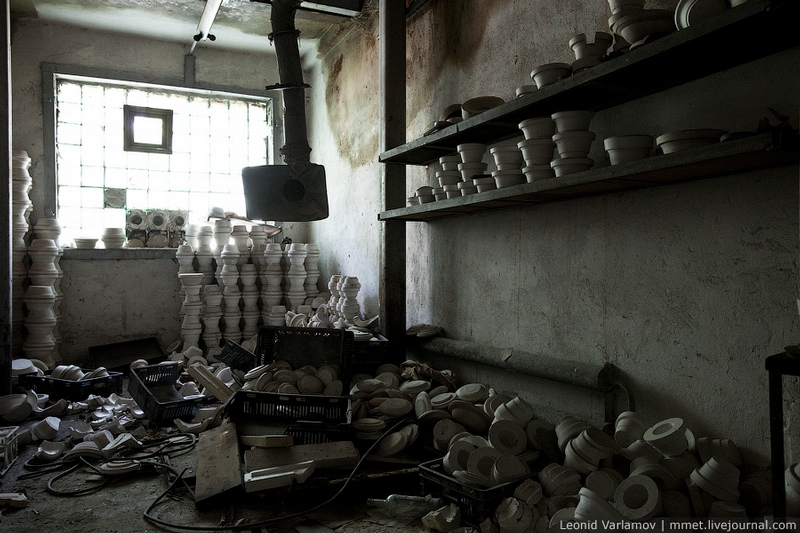
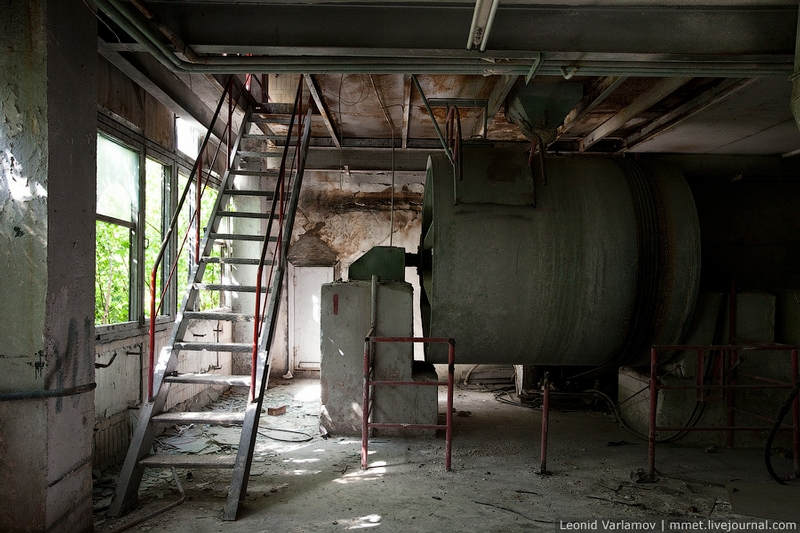
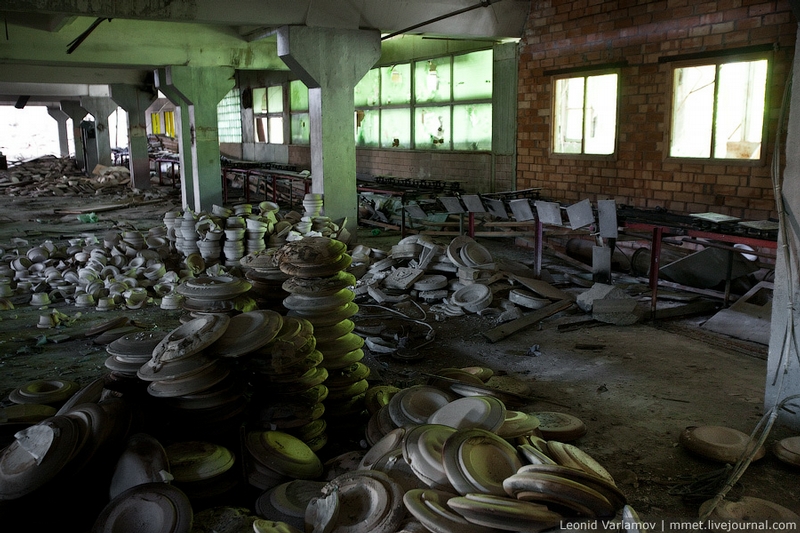
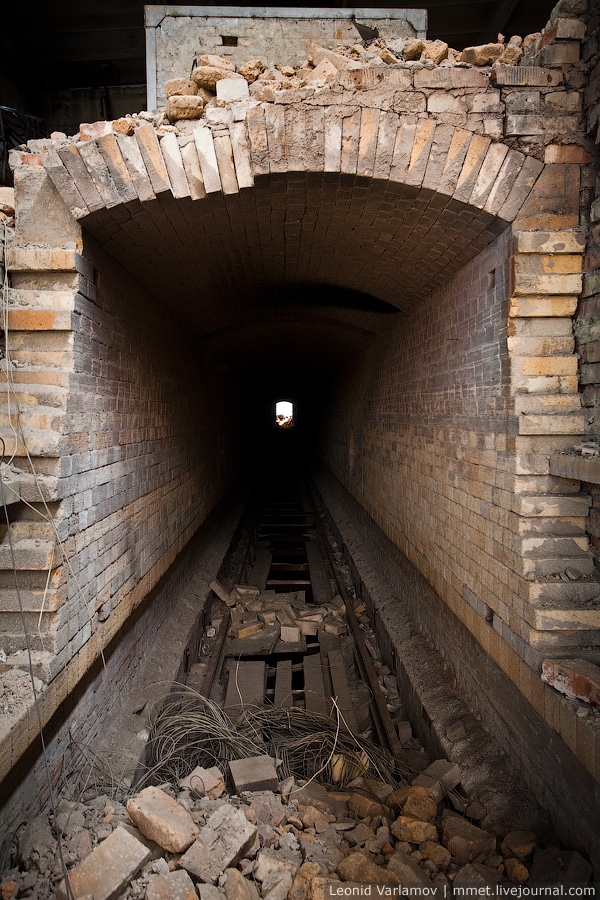
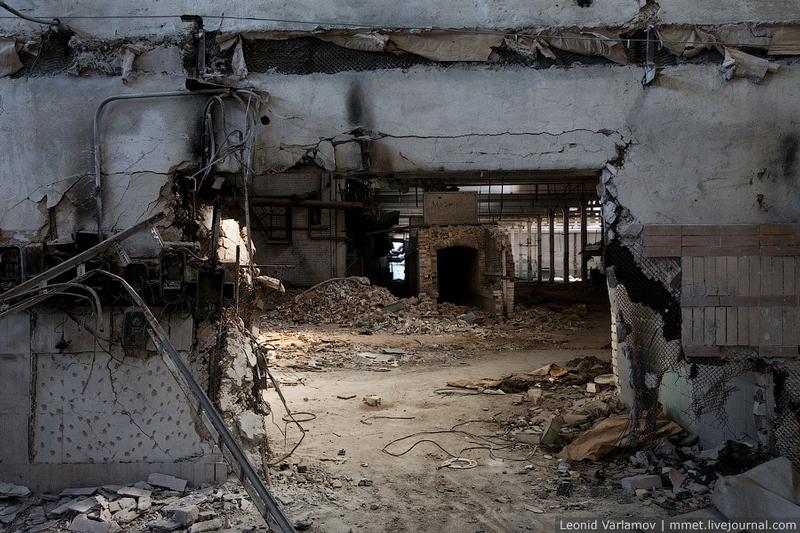
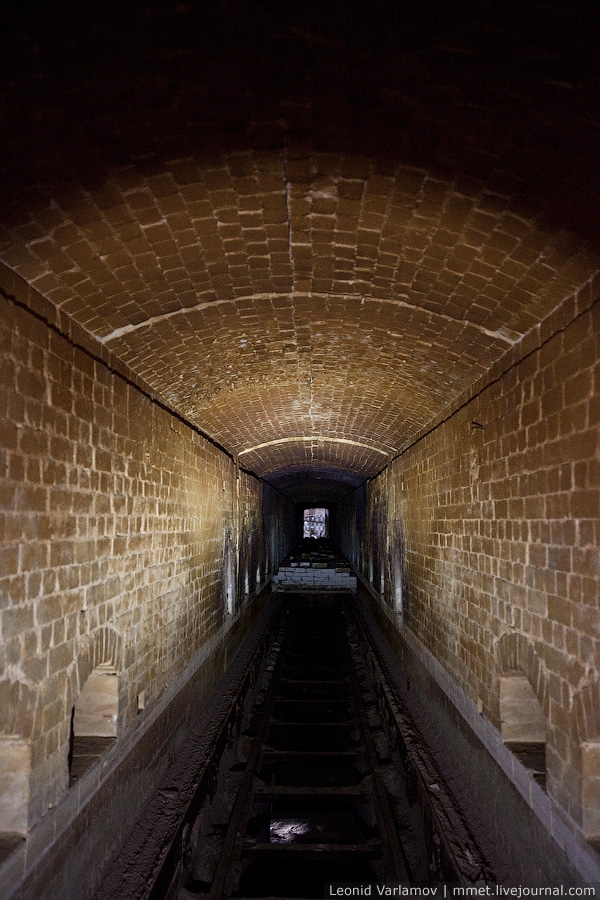
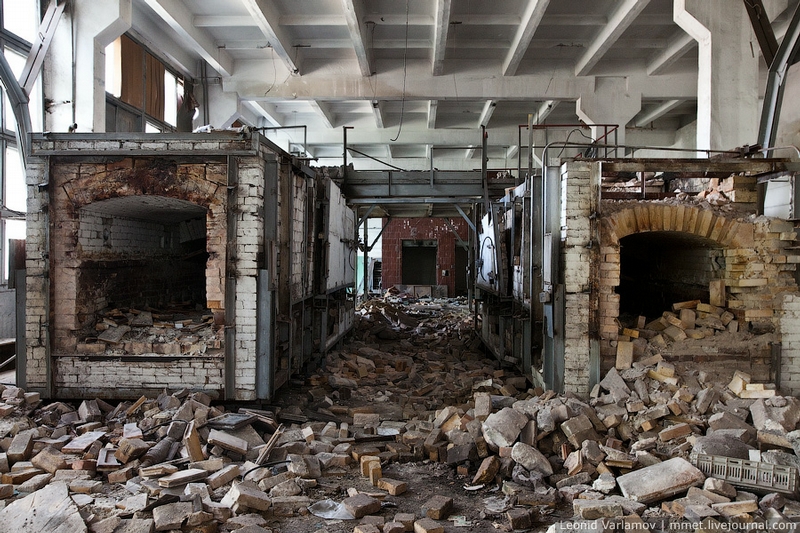
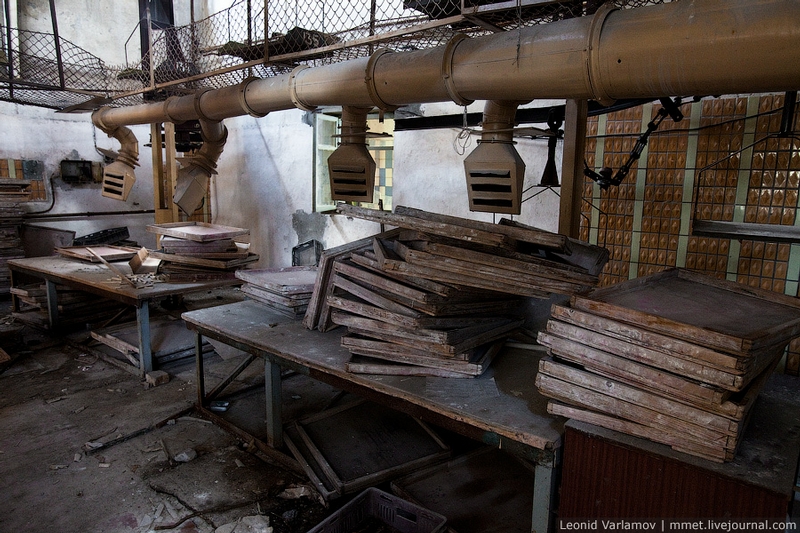
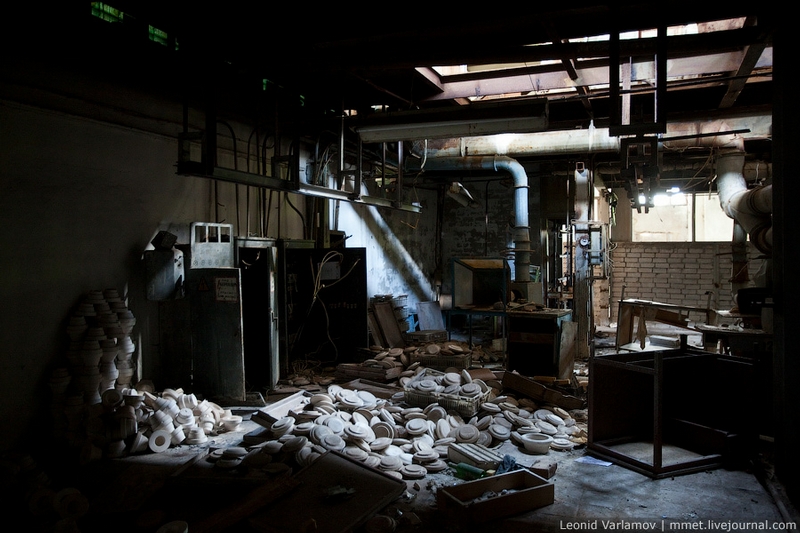
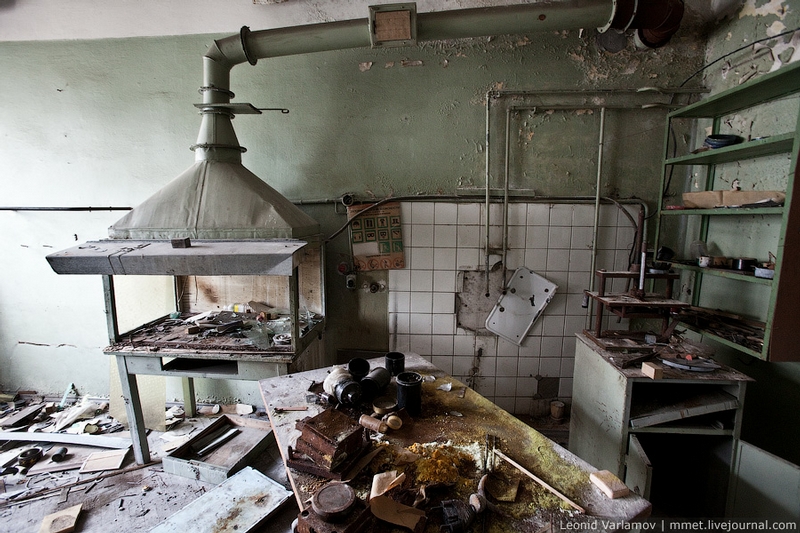
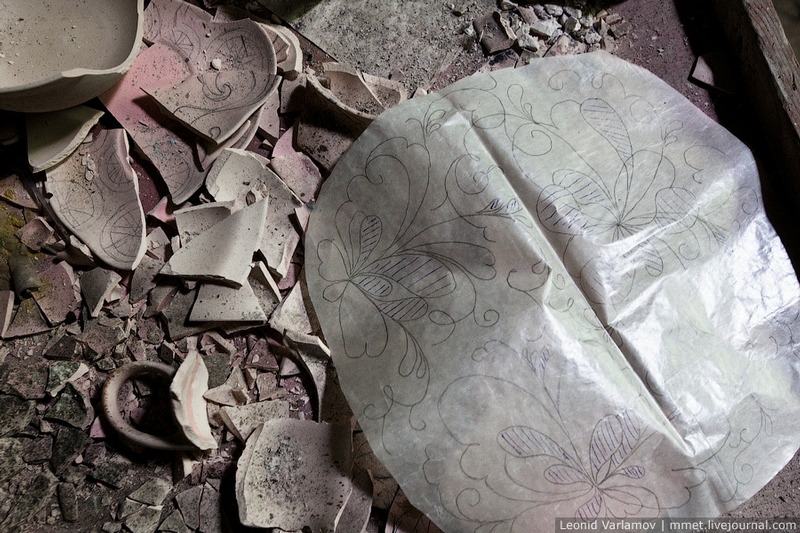
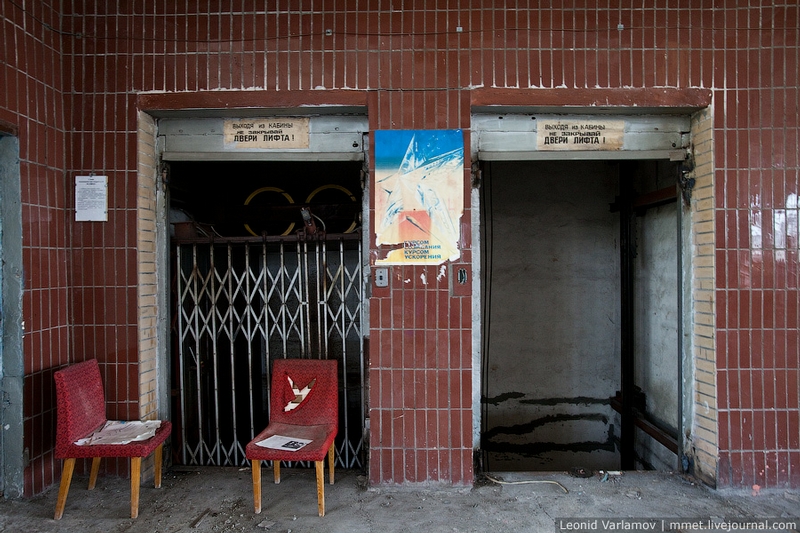
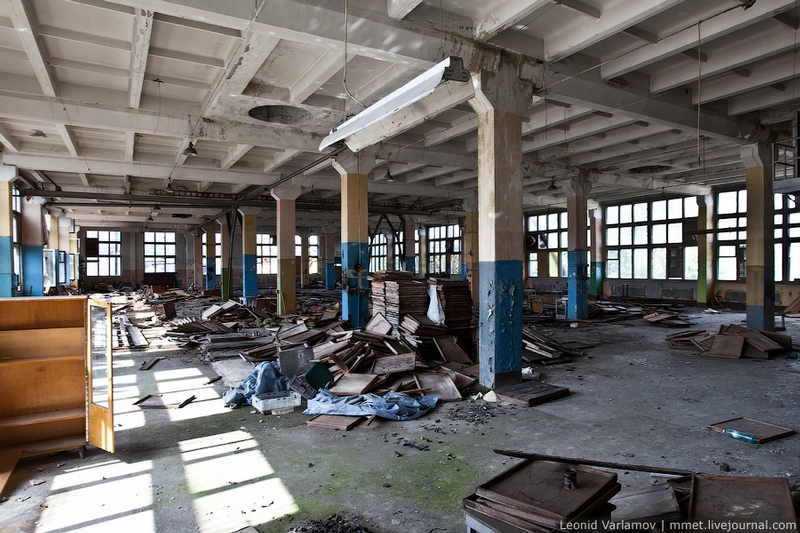
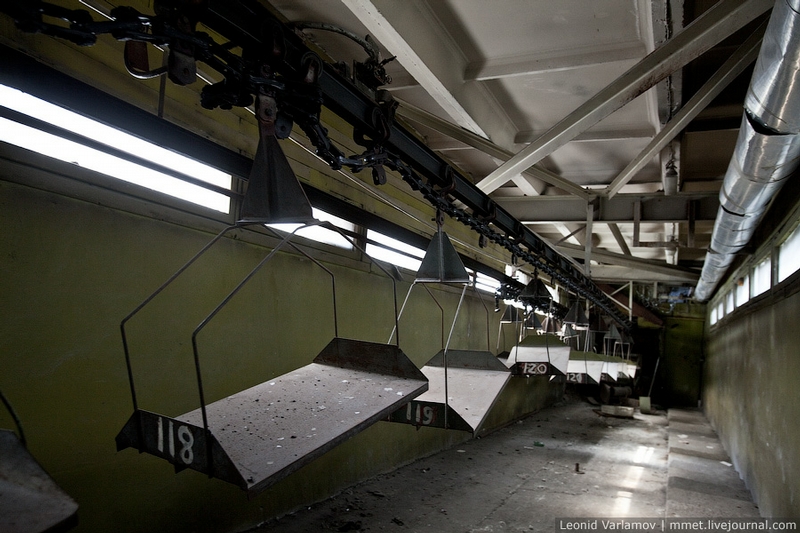

Source ; www.izismile.com
Aucun commentaire:
Enregistrer un commentaire